Leaks
Seems obvious but if you are spending a lot of money every day making compressed air, allowing it to just leak away is literally throwing money away.
- – Leaks can be in the pipework used to feed the compressed air around the building
- – Can be in connections from the pipework to plant and tools that use the compressed air
- – Or can be in the tools themselves
Checking and fixing leaks is probably the most cost effective way of saving energy. Most leaks only require a small modification or replacement of existing or failed pipe or fittings.
Leaks are expensive. A small leak maybe 1mm across, almost too small to see or hear, can cost upwards to 50p in energy per day to feed and remember if this goes on day after day until the leak is fixed. A large leak of maybe 5mm across will cost several pounds a day to feed. Again it will go on day after day costing you money.
There are lots of ways prove the scale of the leaks you have on site.
1/ The simplest is to take a walk round the factory after everyone has gone home and listen to the hissing in the factory coming from the factory air system.
2/ Another way is to wait until everyone has gone home, turn off the compressor and see how long it takes for the air receiver to drain down if after half an hour the air receiver pressure has dropped a lot you probably have some serious leaks in the system! If the pressure remains as it was at the start you are probably ok.
3/ Another, much more accurate and quantifiable way to see how big an issue you have is to get an engineer to come and do an air leak survey. The process of completing an air leak survey is an engineer goes round your factory with a special hand held ultrasonic detector. This very precise measuring device is able to detect extremely small air leaks from the hissing noise at quite a distance. The accuracy of these devices is quite amazing. They can even find small leaks above suspended ceilings or behind partition walls etc.
The air leak detector gives an accurate estimation of the scale of the leak and exactly where on a joint the leak is coming from. A good system will leave the customer with a report showing exactly where the leaks are, which fitting is leaking (often with a photo of the fitting in question), the size of the leak and the cost per hour / day of the leak. Most companies also tag items that are leaking with a permanent tag for easy future identification.
The Air Saver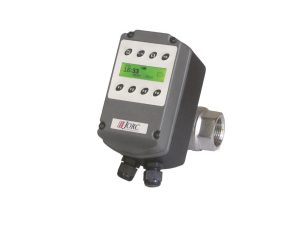
A simple and cheap energy saving solution that some customers like is to fit an ‘air saver’. The air saver whilst not curing leaks does prevent leaks draining you air system overnight. The air saver is a programmable isolation valve that is fitted to the outlet of your air receiver. Once the valve is fitted, you programme it to automatically open before the factory starts in the morning and to automatically shut once the factory closes. This effectively isolates all the downstream pipework and equipment securing all the compressed air in your receiver from being lost overnight through leaks in the downstream system. This is even more important if your compressor doesn’t get turned off at night. The air saver will hold the pressure in the receiver preventing the compressor running all night just to feed leaks.
For the relatively low cost of the ‘air saver’ valve, this is a very cost effective solution to save energy.
Turn the compressor off at night
The other thing that you need to do is to ensure you air compressor does get turned off every night. Turning the compressor off / on can be simplified by fitting a remote start / stop button located somewhere convenient to the factory.
Reduce system pressure
Reducing the overall system pressure has several energy saving benefits. The compressor works less hard, saving energy. Additionally any leaks you may have in your system flow less air, again saving energy.
1/ Compressor energy saving
With a reduced system pressure the compressor doesn’t need to work as hard, saving energy. Additionally, the compressor becomes more efficient since a lower operating pressure reduces losses through leakage within the compression elements. This is best understood if you consider high pressure air is constantly trying to escape around the screws or pistons in a compressor. Modern compressor design reduces this considerably, however, small leakage does occur and this is reduced if the operating pressure is reduced.
Typically for every bar the system pressure is reduced reduces total energy usage by approx 4%.
2/ reduced leaks
Leaks in your pipework system are reduced if the system pressure is reduced. Whilst fixing the leaks is still the best and most appropriate solution reducing the pressure also has a significant effect on wastage and energy consumption.